1前言
無鉛工藝已經廣泛應用,但在軍事電子制造領域仍然采用有鉛的工藝,而元器件卻買不到有鉛的,出現了有鉛與無鉛共存的現象,目前我所有鉛/無鉛BGA器件共同裝配使用較為普遍,而由于有鉛焊球與無鉛焊球的熔點不相同,如采用Sn-Ag-Cu合金的無鉛BGA的焊球熔點較高為217℃,而Sn63-37Pb合金的有鉛BGA的焊球熔點為183℃,如果采用Sn63-37Pb焊料的溫度曲線,一般峰值溫度在210~230℃,假設一個PBGA的峰值溫度為220℃,再流焊時當溫度上升到183℃時印在焊盤上的Sn-37Pb焊膏開始熔化,此時無鉛PBGA的Sn-Ag-Cu焊球還沒有熔化;當溫度上升到220℃時,按照有鉛工藝就要開始降溫、結束焊接了,此時無鉛焊球剛剛熔化,雖然Sn-Ag-Cu合金標稱的熔點為217℃,但實際上Sn-Ag-Cu合金并不是真正的共晶合金,固相線與液相線的溫度范圍是216~220℃,因此,有鉛工藝冷卻凝固結束焊接的溫度恰好是無鉛Sn-Ag-Cu焊球剛剛熔化之時,并處于固、液相共存的漿糊狀態,焊球熔化時由于器件重力的作用焊球開始下沉,在器件下沉過程中稍有震動或PCB微量變形,使PBGA元件一側原來的焊接界面結構被破壞,又不能形成新的界面金屬間合金層,容易造成PBGA、一側焊點失效,由以上可以看出在有鉛/無鉛混合裝配過程中應兼顧兩種焊料的溫度特性,工藝窗口小難度較大。
在混合裝配時要得到焊接可靠的產品就不能只關注裝配焊接環節,而應從裝配的前、中以及后端著手即加強整個過程控制,根據具體情況區別對待,及時調制裝配生產方案使之更有針對性,這樣才能得到可靠的產品,下面既以一個工藝試驗為例,分別列舉了各環節所應注意加強控制的要點。
2工藝試驗
2.1試驗簡介
對于有鉛/無鉛BGA混裝應具體分兩種情況,一是無鉛器件數量居多,或存在尺寸較大的無鉛BGA器件,則采用兼容焊接工藝曲線進行焊接,既是在有鉛工藝曲線的基礎上合理提高溫度,使峰值溫度控制在230~235℃范圍以內,這樣在不損傷有鉛BGA器件的同時滿足無鉛BGA器件回流所需溫度,達到較好焊接;二是有鉛器件數量居多,且無鉛BGA器件尺寸較小,則可通過植球工藝將無鉛器件轉換成有鉛器件進而采用有鉛工藝曲線進行焊接。
在本試驗中共采用兩種試驗板:PCB2、PCB4,試驗板尺寸均為100×150mm,器件采用Sn63-37Pb錫鉛和Sn-Ag-Cu焊球材料無鉛PBGA啞片,PCB厚度為1.6mm。
2.1.1試驗板選用
2.1.2器件情況
PCB2:D2,D3,D5為有鉛啞片,D1,D6為無鉛啞片植球后進行焊接。
PCB4:D2,D3,D7為有鉛啞片,D1,D5,D6,D8為無鉛啞片。
2.2裝配前準備
在裝配前應對印制板和BGA器件本身進行檢查,具體檢查內容如下。
(1)印制板:板面應無明顯的翹曲;焊盤應無短路、斷路情況;焊盤上應無字符、阻焊膜及其它污染;對于氧化嚴重、加工質量低劣、表面污染嚴重及有其它質量問題的印制電路板,不能進行裝配,做不合格品處理(如圖2);對于表面較臟的印制電路板,在焊接前用蘸有無水乙醇的脫脂棉球擠干后清洗2~3次,以確保印制電路板焊接前表面清潔、干凈。
(2)BGA元器件:對待裝配的BGA器件進行有鉛/無鉛判別,并檢查BGA焊球是否氧化以及是否有缺陷。(如圖3)
2.3裝配中
(1)為消除潮氣在焊接高溫中蒸發帶來的不利影響,所以有必要對BGA器件和板子進行預烘處理,具體方法為:將BGA器件放入烘箱120℃,48h;印制板110℃,4h。
(2)在絲印焊膏時,焊膏應覆蓋焊盤75%以上的面積,焊膏表面應光滑、均勻、無空隙、不連涂短接相近的焊盤,不粘污焊盤周圍的基板并且焊膏印刷完到再流焊焊接之間的等待時間控制在2h以內。
(3)設置焊接曲線
需要說明的是以下所列舉的焊接工藝曲線參數是在對本次試驗所使用的印制板所做試驗中得來的,在生產中則應根據實際板子情況:如板子大小、層數,器件種類,器件數量、分布等情況綜合考慮來調整設置焊接曲線。
對PCB4而言,板子上無鉛BGA器件數量多于有鉛器件數量,故考慮設置兼容曲線進行焊接,在對曲線進行多次測試調整后確定參數如表1所示:
表1兼容焊接工藝曲線
單位:℃
帶速:15in/min
對PCB2而言,板子上有鉛BGA器件數量多于無鉛器件數量,且無鉛器件D1較小,故考慮先對D1、D6器件進行植球處理,轉換成有鉛器件后再設置有鉛工藝曲線進行焊接,在對曲線進行多次測試調整后確定有鉛焊接工藝曲線參數如表2所示:
表2有鉛焊接工藝曲線(單位:℃)
帶速:15in/min
焊接完成后對兩塊試驗板(PCB2、PCB4)進行X-Ray檢測,BGA器件均沒有短路,印制電路板表面也沒有有斑點、裂紋、氣泡、炭化、發白等現象。
3可靠性驗證
為驗證其可靠性對試驗板進行了各項可靠性試驗和分析測試。
3.1可靠性試驗
完成焊接后對兩塊試驗板進行了溫度沖擊和隨機振動耐久試驗,整個試驗過程中試驗板外觀良好,均未出現異常問題,具體試驗條件見下表:
溫度沖擊試驗:
3.2可靠性測試
為了更深入了解焊點情況,將試驗板送至賽寶實驗室對BGA器件焊點進行了切片、電鏡和染色分析試驗。分析圖片如下:
3.3分析結論
由以上圖片可以看到試驗板混合組裝的有鉛和無鉛BGA焊點的IMC厚度均在1~3μm間,且形態較好,沒有紅色顏料滲透到元件一側或印制板一側界面中,表明沒有虛焊的產生。
4結論
IMC金屬間結合層的形成雖然是焊接良好的一個標志,但過厚或過薄的IMC均會降低焊點力學性能和熱疲勞性能進而影響焊點可靠性,目前普遍認為焊點的IMC在1~3μm間,其結合強度及可靠性相對較好,因此在焊接過程中保障良好的IMC是實現良好焊接的重要條件。
隨著無鉛化的發展,有鉛/無鉛混合裝配難以避免?;旌涎b配由于兩種焊料不同溫度特性,焊接工藝窗口較小,難度較大,但只要加強各個環節過程控制,仍可以得到焊接可靠的產品。
責任編輯人:CC
-
BGA
+關注
關注
5文章
549瀏覽量
47049
發布評論請先 登錄
相關推薦
無鉛焊錫有什么特點?
采用無鉛(Pb)裝配流程裝配高含鉛的DS2502倒裝芯片
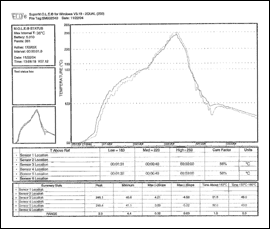
采用無鉛(Pb)裝配流程裝配高含鉛的DS2502倒裝芯片
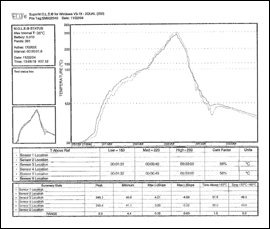
評論