應用現狀
智能制造是支撐我國制造業轉型升級、高質量發展的國家戰略,CPS(信息物理系統)是支撐信息化和工業化深度融合的一套綜合技術體系。DT(數字孿生)技術是智能制造發展的新趨勢和重要抓手,其特征是物理對象的數字化虛擬建模與決策分析,在產品生產環節和智能執行領域,可將其狹義理解為一種實時 CPS。參考德國工業 4.0 關于柔性自動化線的本質,就是通過硬件資源的離散化、服務化封裝,構成一個“服務聯網”的 CPS 網絡系統,這些服務有層次并且能夠動態組合配置,具有明確的數字孿生內涵。
另一方面,從工業數字孿生的應用現狀看,國產自主技術的成功案例主要集中在設備級的應用方面,利用三維模擬展示和非實時雙向異步控制模型,通過數字孿生系統的分析,完成設備的故障分析、壽命預測、遠程管理等功能,主要用于設備的故障診斷、預測性維護、運行參數優化等。產線級、工廠級的應用發展緩慢,缺乏深度。
需求分析
某蓄電池制造企業,6 條自動化產線建造于 2000 年前后,可支持 16 個品類近 100 種工業及民用蓄電池的生產,每條產線在經過換線調整后,適用于 3~5 個品類的自動化連續生產。隨著多品種小批量的沖擊,高昂的換線成本與自動線帶來的質量穩定高速生產之間的矛盾越來越劇烈,該企業只能進一步提高產品的標準化和系列化,對于實在無法滿足的品類市場只能逐步縮減放棄該領域。
大量制造企業在批量實施自動化產線后遇到的困境也與其類似,對智能制造的核心訴求集中在通過面向生產的智能管控,實現連續穩定的混線交叉自動化生產??梢詭砉澕s新產線投資、減少換線次數、節約人力成本、節省試制費用和大幅提高產能等直接經濟效益,同時也具有大幅降低客戶訂單響應時間、起單量無下限、新品拓展無限制等間接效益。
某半導體封裝企業立項研發一種基于控制中心 +PLC的單元組合型智能封裝系統,實現搬運、點膠和固化等設備之間的功能、參數相匹配協調,有效提高設備利用率、封裝效率及封裝品質,實現繁重重復的手動封裝作業向自動化、信息化、智能化的轉型升級。其技術路徑則是將機器人搬運單元、自動點膠單元和自動固化單元等系統封裝為獨立 CPS 單元,通過數字孿生模型的建立,基于控制中心的時序控制和聯動協調達到各子系統功能的融合。
某大型機械設備廠商,希望通過對傳統壓鑄機的控制智能化,達到向數字裝備轉型升級的飛躍。研發內容除了傳統控制領域的基礎功能(壓鑄機速度、壓力、位置閉環控制算法,伺服運動控制板卡等),更重要的是需要采用 Java 或者其他高級語言開發前端上位機系統及后端邏輯控制,并通過壓鑄單元集成智能控制實現壓鑄機單元生產管理、故障診斷、預測分析、再線品質檢測、智能調節工藝參數。其本質就是要建立面向生產的數字孿生體并達到軟硬一體化的智能管控。
由以上分析可以看出,隨著智能制造的深入,裝備生產企業和最終制造企業都不滿足于數字孿生僅僅提供三維模擬演示、離線仿真、技能培訓、遠程運維等淺層次應用,無論是設備級還是產線級,都提出了真正面向生產環節的智能管控功能需求。而按照智能制造核心理念 CPS 的思路,面向生產環節的智能管控需滿足以下技術特征:面向生產運行的持續狀態感知、面向生產異常的分析推理決策、基于生產軟硬件系統集成的閉環執行;并需要具備相應的能力要素。
要滿足以上需求,陳曉紅指出須重點實現生產系統多源異構數據互聯互通和智聯管控,陶飛教授在 2019年工信部開展的工業互聯網創新工程啟動時,更詳細論述了重點技術突破。筆者結合二十余年在制造業信息化的現場工作,進一步認為實時高頻多維關聯模型的構建和毫秒級計算求解更是其中最關鍵的制約。針對此瓶頸,和唐數智發布了國內首款軟硬一體化柔性智能管控引擎HT-CPS(v1.0),以智能制造裝備(全自動機臺、自動化產線和智能執行器)的智能管控為對象,滿足智能制造實時高頻、柔性關聯及多維閉環的技術需求,達到零待機混線交叉生產的實效。在實際工廠生產案例中,應用效果達到國際先進水平。產業化后,可賦能裝備生產商批量提升裝備自動化智能水平,并進一步賦能制造企業低成本應對多品種、小批量、個性化市場需求。工業設備數字孿生應用落地分析見表 1。
技術特征
HT-CPS 柔性智能管控引擎是調度與控制的一體化,隱含了分析決策功能,其原理如圖 1 所示。通過數字虛體給物理實體賦予了一個大腦,稱之為“控制腦”,實現了真正的“虛實映射”“以虛控實”。通過閉環控制將工業互聯從單向的數據狀態傳輸推向了雙向的自動控制,將 DT 模型的應用從監視推向了管控,將偏硬的 DCS 控制和偏軟的 APS 調度相結合,達到軟硬一體化智能管控的目標。針對智能制造需求,具有以下技術特征:
①實時,基于物理單元實體的實時狀態得到的數字虛體的映射;②高頻,滿足生產過程監視、監控和自動化控制,毫秒級的時間響應;③多維,將物理對象的幾何/物理/行 為/規則及約束的多線程、不同粒度的多層級、推進演化 /實時過程/外部干擾的多時間等維度進行了綜合建模,并對其求解進行選優配置;④柔性,將硬件資源離散建模進行服務化封裝,通過實時調度控制算法,實現制造執行單元鏈條的重構與控制;⑤關聯,任何需要建立關聯的構成要素裝置,能夠實現聯動控制和時序協調,從而滿足自動化混流交叉生產;⑥閉環,DT 模型發現物理實體狀態在時空域和邏輯域的內在因果性或關聯性關系,權衡判斷當前時刻獲取的多維信息,通過調度控制算法,形成最優決策,通過調度、預警和通信連接等多個線程,模型和算法以毫秒級的響應頻率,支持完成整個閉環控制。
運行邏輯及理論突破
DT 模型的構建,是將制造資源離散化、服務化封裝后,搭建多層級的多 Agent 結構,并根據智能制造裝備的柔性化快速重構需求,對資源鏈條進行動態的重構執行一體化控制?;趯崟r的狀態驅動,Agent 主要完成四類任務:一是根據工藝執行的規則機理對當前的實際執行狀態的正確與否進行判定;二是在實際執行狀態輸入的驅動下,通過分析推理決策對實際工藝執行參數進行修正和優化;三是結合某一周期內動態變化的實際執行狀態對生產系統進行糾偏或優化,提供持續優化的資源配置決策方案;四是以前三類的數據為樣本,對生產執行穩態運行的持續態勢進行判斷。
4.1 運行邏輯
1)數字孿生模型的構建。普遍的方法是從三維仿真入手。即技術切入點在數字孿生成熟度模型的 0~1 級,從一個系統的幾何結構開始建模,先取得相似的幾何模型,逐步向里面的機理模型深入,容易卡殼在“虛而不擬仿而不真”;HT-CPS 引擎是先把機理全部對象化再實現智能管控,“控制腦”做出決策以虛控實并可以動態重構。是從 4~5 級構建,從里往外發展,已突破技術路徑瓶頸。
HT-CPS 柔性智能管控引擎將物理對象的幾何/物理/行 為/規則及約束的多線程、不同粒度的多層級、推進演化/實時過程/外部干擾的多時間等維度進行了綜合建模,并對其求解進行選優配置。并行協同約束的優化算法,其中調度域主要對象有:工件類(組別/個體)、工位類(組別/個體)、時間類(進入/運行/退出)和工藝路線類(工位/順序),控制域主要對象有工藝參數類(閾值/接受條件)、加工狀態類(在制/空閑)和預警類(正常/報 錯/呆滯)。DT 模型對象類表見表 2。
2)狀態驅動。狀態驅動的根本思想,與 C++ 面向對象編程一致,即把一個對象的行為分解為易于管理的“塊”或者狀態。組織和進行狀態轉換的機制采用狀態轉換表。Agent 隔一定時間查詢這個表格,以使得它能夠基于從系統環境接收到的消息來進行必須的狀態轉換。每一個狀態都能夠實現為彼此分離的與 Agent 不耦合的對象或函數,以提供清晰和可伸縮的架構。機械手狀態轉換示意見表 3。
反應式動態調度(毫秒級)。智能制造裝備(全自動機臺、自動化產線、智能執行器)高頻實時的需求特征,使得傳統的以資源特定時間段的占用作為計算核心的 APS不具有可執行性,根據狀態驅動的處理策略,HT-CPS 以“長控制 + 短控制”相結合的方式來實現反應式動態調度。在50ms 以內的一個周期,獲取全要素的多維環境信息,在線求解一個有限時域的半閉環優化問題,并將得到的控制序列的第一個元素作用于被控對象,完成控制閉環。
4.2 理論突破
分鐘級的工序調度和毫秒級的工藝執行,在算法中實現了融合控制;通過工件、工位、工作單元、工藝參數、加工狀態、防呆防錯六個自由度關聯,實現了工藝執行的動態可重組,基本涵蓋當前智能裝備對柔性自動化的全部需求;以此為基礎,進一步將需求轉化為規則因子,執行提升為能力態重組,從數據關聯(數字可計量)上升為特征關聯(能力可度量),有望實現真正的工業 AI。
案例介紹及應用方向
5.1 案例介紹
某高新科技行業重點裝備,屬機器人 cell 類型全自動機臺,人工/上料機上料后,可自動完成整件加工工藝中的一段如圖 2 所示。機臺中央為雙臂機械手 R,完成工件所有的位置轉移。工藝路線涉及 5 類工位(A~E),可設定一組工件采用同一工藝路線,也可為每個工件設定獨立的工藝路線,從而滿足訂單極限個性化(單件流)需求。
各工位處理單元數不等,可以根據生產效率需要增刪。同組工位的工藝參數控制指標相同,不同工位的加工時間為 5~180s 不等。每個加工單元通過 PLC 組成控制閉環,PLC、R 與 HT-CPS 引擎通過工業以太網通信,整個機臺的協調控制由引擎實現。防錯防呆響應為毫秒級,報錯或停止后,可一鍵恢復延續加工。
調度控制目標設定為動態工藝路線下 R 的效率最高(根據用戶需求設定),等同于單位時間內總產出最大。目前十臺套在實際生產中,零待機完成混線交叉生產,設備不間斷工作時間達 720h,故障率< 0.1%,產品質量穩定合格率> 99.99%,連續混線加工穩定產出率 150 件 /h,達到同等國際領先水平。
5.2 應用方向
1)多工序高集成度自動化機臺。行業裝備生產商可在上位機集成 HT-CPS 引擎,形成行業通用方案,全面提升行業裝備智能化水平。
2)剛性自動化線的柔性升級。傳統自動化線適用于大批量單一品種的高效生產,但產線切換復雜,難以應對小批量、個性化市場需求,可集成 HT-CPS 引擎快捷升級為模塊化設備蜂巢布局的柔性可重構生產線,如圖 3所示,大幅節省投資、提升效率。
3)智能執行器向高精度多目標升級。在復雜環境工作帶有中央控制器的智能終端,可部署 HT-CPS 引擎,提高多維變量的感知和處理能力,通過智能管控的結合提高執行精度,并實現多目標混合執行路徑的自決策和自優化。
戰略價值
未來 AI 制造需要的支撐是一個復雜狀態多維巨系統,其本質是將不可度量不透明不可控,向規?;挠行蜣D變。不僅是可見的實體及其之間的聯動關系,更重要的是背后看不見的各種策略與規則,以及信息、通信與自動化控制三者的(ICT)深度融合,即機理模型(DT)的建立、輔助決策(管理決策、調度決策和工藝決策)并自治執行。這也是工業軟件需要長期技術沉淀和知識積累的方面。基于對硬件離散化之后的軟件外殼封裝是工業 4.0 的核心精髓,HT-CPS 引擎提供的正是構建這種分布式增強網絡型系統的“控制腦”,將與“工藝腦”“調度腦”共同構成工業大腦的腦干。
發展自主可控的數字孿生智能制造系統,對于我國制造業轉型升級、由大到強至關重要。國內現在有很多團隊投入和推出了建模、仿真、調度類軟件,APS 與 DCS的邊界正在逐漸融化,未來工廠以實際狀態的三維模擬展示為主,這是個良好的開端,而要實現國產工業數字孿生的應用突破,必須將場景從“仿真”推向“管控”。在這種時代背景下,作為首款聚焦軟硬一體化柔性智能管控結合的支撐類軟件,HT-CPS 引擎的推出,相信會為我國工業軟件的整體加速起到良好的推動作用。
審核編輯 :李倩
-
仿真
+關注
關注
50文章
4124瀏覽量
133993 -
智能制造
+關注
關注
48文章
5612瀏覽量
76565 -
數字孿生
+關注
關注
4文章
1342瀏覽量
12360
原文標題:從仿真到管控:突破國產工業數字孿生應用瓶頸
文章出處:【微信號:CADCAM_beijing,微信公眾號:智能制造IMS】歡迎添加關注!文章轉載請注明出處。
發布評論請先 登錄
相關推薦
數字孿生是什么?
基于仿真的數字孿生系統構建與應用
數字孿生是指什么
工業4.0與數字孿生
數字孿生是什么,有什么應用
數字孿生屬于元宇宙概念嗎
數字孿生將加快工業虛擬化和AI時代的到來
從網絡仿真到數據中心數字孿生
仿真技術與數字孿生的關系及未來
解碼國產EDA數字仿真器系列之一 | 從零到一 如何構建一款先進的數字仿真器
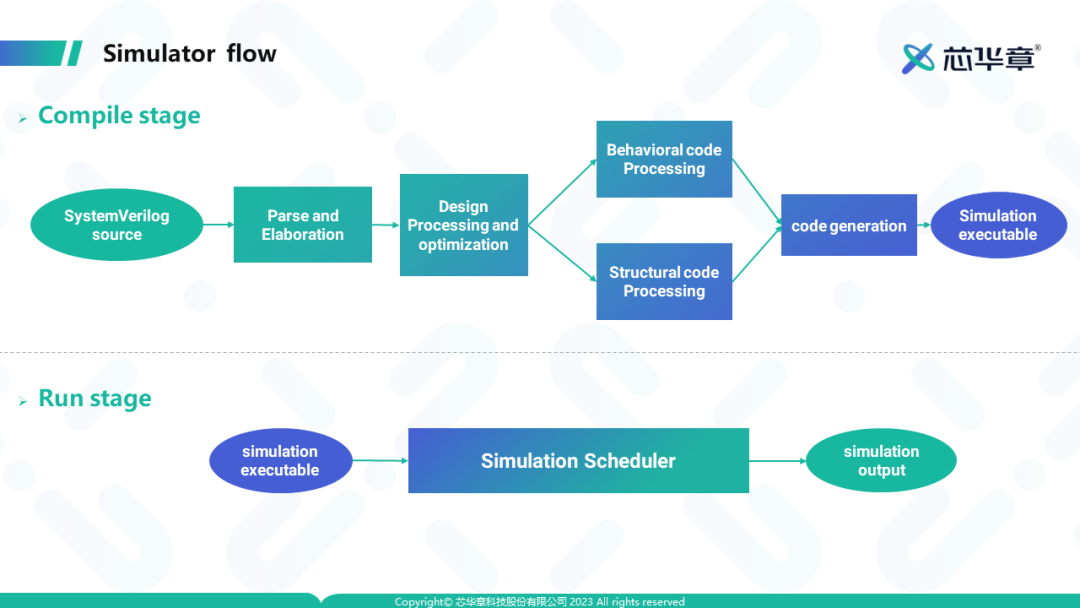
評論