摘 要:通過對薄膜電路制備工藝系統的研究,將傳統的薄膜電路制備工藝與犧牲層技術相結合,提出了一種新型的薄膜電路制備方法。克服了對反應離子刻蝕及離子束刻蝕等干法刻蝕設備的依賴,同時取消了濕法刻蝕,避免了其對圖形精度的影響。通過優化光刻膠配比,調節噴膠速率和采用濺射后退火等手段解決了犧牲層線條模糊、孔洞出現和膜基結合力差等問題。采用光刻膠犧牲層技術可以制備出高精度薄膜電路。
薄膜基板是一種高精度和高集成度的電路基板,制備流程通常采用物理氣象沉積種子層,利用光刻與刻蝕的圖形化手段實現布線,最后采用電鍍工藝對線路進行加厚,從而在陶瓷基材上制備出微帶電路圖形。
薄膜電路基板由于采用了光刻與刻蝕的圖形化手段,從而能夠實現高密度和高精度布線。薄膜基板互聯密度高,并且能夠在基板內部實現電阻、電感和電容等無源元件的集成,在實現微波電路的裝配中,采用薄膜基板實現封裝,整個結構具備分系統和系統級功能[1-2]。
其中刻蝕是指利用物理或者化學方法將未受光刻膠圖形保護部分的材料從表面逐層清楚的過程。
刻蝕的方法主要有干法刻蝕與濕法刻蝕兩種。干法刻蝕是指利用等離子體放電產生的物理與化學過程對材料表面進行加工[3]。干法刻蝕可以實現高精度的電路圖形,但是對設備依賴高,需要反應離子刻蝕或者離子束刻蝕等成本極高的工藝設備。
濕法刻蝕工藝是采用化學試劑利用化學反應對未覆蓋有光刻膠的金屬裸露區域進行腐蝕,濕法刻蝕具有成本低和速率快的特點,刻蝕線寬一般為50 μm,刻蝕效率顯著優于干法刻蝕[4]。然而,濕法刻蝕由于是各向同性的化學反應,在向下刻蝕的同時會產生側腐蝕現象,制作出的電路線寬精度在±10 μm級別。
另外,腐蝕液會從圖形側方浸入到膜層與基板之間,從而影響薄膜與基板之間的結合力。在蝕刻Cu層和Cr層之后,需要去除光刻膠殘留物。限于目前的實驗條件,只能使用濕法刻蝕,提高圖形精度成為亟需解決的問題。
犧牲層技術是一種廣泛應用于MEMS(MicroElectro Mechanical Systems,微電子機械系統)中的微納工藝手段,由于不同材料對同一刻蝕液和刻蝕氣體敏感程度不同,刻蝕速率也不同,因而可以選擇性地將有刻蝕需求區域的材料(也稱為犧牲層)刻蝕掉,然后將空腔結構釋放掉,從而制備出各種懸空結構[5]。
使用光刻膠作為犧牲層有以下優點:
1)光刻膠本身的理化特點決定了其容易成膜,利用勻膠或者噴膠的方法能較為輕易地獲得厚度可控的犧牲層;
2)犧牲層材料必須要能容易地刻蝕或溶解掉,而光刻膠易溶于堿性溶劑或者丙酮,在完成了圖形制備后能夠較為容易去除;
3)在使用其他材料當做犧牲層時,依然需要采用光刻膠通過光刻與刻蝕的方法來獲取圖形化的犧牲層,所以直接用光刻膠當做犧牲層比用其他材料做為犧牲層工藝簡單。
將光刻膠犧牲層技術與傳統的薄膜電路制備工藝相結合,則有可能提高電路圖形精度,減少制作工藝步驟[6]。
1 光刻膠犧牲層工藝
傳統薄膜電路制作的流程為激光打孔,清洗基板,基板金屬化,制作圖形(涂膠、曝光和顯影),濕法刻蝕,去光刻膠,電鍍加厚,如圖1所示。
其中激光打孔用于實現基板正反兩面互聯,為了保證孔的深寬比,以及熱影響區不至過大,通常會使用能量較小的紫外激光完成通孔的加工。基板金屬化是在陶瓷基底上采用物理氣相沉積的方式沉積一層厚度約為幾百nm的種子層,以便于后續電鍍加厚的實現。
在完成了表面金屬化之后,實現表面電路圖形的制作需要采用光刻與刻蝕的工藝手段,首先,將稀釋后的光刻膠采用噴涂的方式均勻地涂覆在基板表面,然后在掩膜下進行曝光和顯影,即可制備出電路圖形,接下來帶著光刻膠掩膜進行電鍍,將圖形厚度加厚至需要的厚度,然后清洗掉光刻膠掩膜,最終將未被加厚的非電路圖形區域的種子層金屬刻蝕掉,完成薄膜電路基板的制備。
由于采用了噴涂工藝,使用了經過稀釋的光刻膠,稀釋后的光刻膠耐電鍍液腐蝕性能不良,導致電鍍時圖形模糊,線路精度無法滿足要求。如果在光刻刻蝕后先進行刻蝕,由于采用了濕法刻蝕工藝,將導致種子層出現側腐蝕現象,同樣精度無法達標。
因此,通過引進光刻膠犧牲層技術,改進薄膜電路的制備流程,具體流程為激光打孔,清洗基板,制作圖形(涂膠、曝光和顯影),正面濺射種子層,去光刻膠,反面濺射,電鍍加厚,如圖2所示。
改善之后的工藝與之前最大的區別在于使用光刻膠充當濺射的掩膜,在電鍍之前將電路圖形高精度的制備出來,不再進行濕法刻蝕,避免了側腐蝕對線條精度和膜基結合力的影響,同時,基板只浸入丙酮中一次以去除光刻膠,避免了大量溶液的使用,減小了溶液對電路圖形表面的氧化作用,提高了圖形表面的親水性和電鍍工藝的可靠性。
2 工藝分析與改進
本文中選取AZ4620光刻膠,黏度為400 mPa,由于薄膜基板上有通孔的存在,采用旋涂工藝實現光刻膠的涂覆將無法在孔壁均勻成膜,因此需要采用噴涂的方式來完成光刻膠的涂覆,而噴涂則對光刻膠的黏度有較高要求,通常情況下黏度不宜大于40 mPa,黏度過大則難以實現光刻膠的霧化,進而無法噴涂,這就需要將光刻膠稀釋后才能進行噴涂。常用的稀釋劑為丁酮與丙二醇甲醚醋酸酯(propylene glycolmethyl ether acetate,PGMEA),對稀釋后的光刻膠進行噴涂實驗,結果如圖3所示。
圖3為不同配比的光刻膠經過顯影曝光后的圖形照片,其中圖3(a)為優化前光刻膠圖形照片,可以看出,邊緣線條粗糙,光刻膠被溶解掉。傳統用于噴涂的光刻膠是作用在金屬上,圖形化后進行刻蝕,而金屬與光刻膠結合力和陶瓷基板與光刻膠結合力有所不同,同時基體材料的不同,其對光的敏感程度也有所不同,直接利用該配比的光刻膠噴涂,曝光顯影后將會導致線條邊緣塌陷,光刻膠被溶解等情況,無法滿足需求。
通過開展工藝實驗,摸索合理的配比,經優化之后的光刻膠圖形照片如圖3(b)所示,可以看出,圖形精度有所改善,但繼續放大后(如圖3(c)所示)線條邊緣仍有鋸齒狀,過細的線條依然被溶解掉。與已經沉積了金屬種子層的基板表面相比,未沉積薄膜前的陶瓷基板表面異常光滑。
時,噴涂使用的是稀釋后的光刻膠,由于稀釋劑的加入,其對紫外光的透過率增大。曝光時,紫外光穿過光刻膠到達基板表面產生反射,使得被掩模遮蓋邊緣處的光刻膠接觸到紫外光,經過顯影后被溶解掉,使得線條成鋸齒狀。
分析原因,有可能是經過稀釋后的光刻膠里包含的溶劑過多導致,于是希望通過增加前烘時間,降低光刻膠里溶劑的含量,從而減小由于基板表面紫外光的反射帶來的影響。圖4為增加了前烘時間的光刻膠圖形照片,可以看出線條邊緣陡直,無鋸齒,效果良好。
由于不同的光刻膠性質不同,對于不同種類以及不同配比的光刻膠,進行光刻膠的涂覆時,采用的噴涂速率曲線也將有所不同,配比優化后原先的噴涂速率曲線已不再適用,有必要對稀釋后光刻膠重新確定其噴涂速率,具體方式為通過調整噴嘴運行至不同區域時的速率來調節噴涂速率曲線。
在噴涂過程中,為了保證膜厚均勻,噴嘴在運動時掃描速度應不斷變化。當噴嘴掃描至基片邊緣的位置時,由于周長最大,掃描速率應最小,當噴嘴掃描至基片中心的位置時,由于周長最小,掃描速率應最大。圖6是光刻膠噴涂速率曲線,圖6(a)為未經
稀釋的AZ4620光刻膠噴涂速率曲線,采用此曲線使用稀釋后的光刻膠進行噴涂,噴涂后的光刻膠分布不均,表面明顯存在高度落差,呈現出中間薄兩邊厚的形態,圖6(b)為優化后的噴涂速率曲線,光刻膠均勻分布,厚度一致。
傳統的種子層濺射工藝需要在250 ℃以上進行,以提高膜基結合力。但是光刻膠無法承受如此高的溫度。在該溫度下,光刻膠會出現氧化、變質和氣化等不利情況。經過稀釋后的光刻膠更是無法承受此問題。本研究通過工藝試驗,確出濺射時光刻膠可以耐受的溫度,通過提高本底真空來提高膜基結合力,另外在完成了正面的濺射后,將光刻膠去除,然后進行反面濺射,反面濺射時選擇較高的腔體溫度,該過程可以看作對正面濺射的種子層進行后續退火,從而提高了膜基結合力。
在采用犧牲層技術,完成了整個薄膜電路基板的制備后,按照QJ497-1990標準要求對采用光刻膠犧牲層技術前后制備的薄膜電路進行了附著力測試。未采用光刻膠犧牲層技術制備的薄膜電路出現了嚴重的側腐蝕,電路圖形與基板結合力差,測試時鍍層出現分層。采用了光刻膠犧牲層技術制備的薄膜電路線條陡直,圖形與基板結合力良好,鍍層未出現分層。
3 總 結
本文將光刻膠犧牲層技術與薄膜電路基板制備工藝相結合,對傳統的薄膜電路基板制備工藝進行了改進和優化。通過選擇合適的光刻膠配比、優化噴涂速率曲線和采取后續退火等手段解決了電路圖形模糊、附著力差和易氧化導致電鍍效果差等問題,最終得到了性能良好的薄膜電路基板,膜基結合力滿足國標要求。同時,克服了對昂貴干法刻蝕設備的依賴,避免了濕法刻蝕對線條精度的影響,降低了薄膜電路的制作成本,提高了產品合格率
審核編輯 :李倩
-
電感
+關注
關注
54文章
6153瀏覽量
102688 -
光刻膠
+關注
關注
10文章
321瀏覽量
30346 -
薄膜電路
+關注
關注
1文章
6瀏覽量
2949
原文標題:采用光刻膠犧牲層技術改善薄膜電路制備工藝
文章出處:【微信號:中科聚智,微信公眾號:中科聚智】歡迎添加關注!文章轉載請注明出處。
發布評論請先 登錄
相關推薦
Futurrex高端光刻膠
光刻膠殘留要怎么解決?
Microchem SU-8光刻膠 2000系列
光刻膠
光刻膠在集成電路制造中的應用
《炬豐科技-半導體工藝》光刻前 GaAs 表面處理以改善濕化學蝕刻過程中的光刻膠附著力和改善濕蝕刻輪廓
光刻膠與光刻工藝技術
晶片清洗、阻擋層形成和光刻膠應用
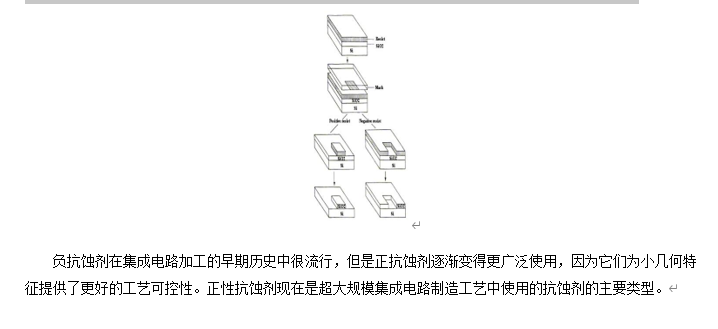
光刻膠的原理和正負光刻膠的主要組分是什么
光刻膠黏度如何測量?光刻膠需要稀釋嗎?
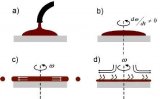
評論