電子設備設計中功耗、尺寸和溫度的演變
過去,導致系統故障的主要原因是關鍵元器件過熱。在一些系統的最熱點上,半導體結溫可能達到 150°C或更高,非常接近其工作極限。如若未從芯片上移除過多的熱量,這種高溫會修改并最終破壞電路的運行。但失效分析表明,在現如今的系統設計中,這并不是唯一的問題。
典型元器件故障也可能由重復發生的瞬態熱引起。加熱和散熱會在封裝結構(固晶焊、焊點)中的材料界面處引起剪切應力,從而導致分層、撕裂等。而由此導致的接觸面積減少將會引起熱量移除不足,進而可能造成熱失控。
散熱是一種三維效應
長期以來,封裝電子元器件在產品說明中均使用單一熱阻表示。功率器件通常密封在具有專用散熱表面的封裝中,我們將其稱為“外殼”。在分立半導體(二極管、晶體管)中,器件最熱的部分是 PN 結。初步評估時,工程師同意,安裝封裝的表面上方的結溫升幅等于所提供的熱阻乘以所施加的功率。
在常規電子設備以及固態照明中,結溫 (TJ) 是影響系統可靠性和使用壽命的主要因素。LED 的結溫是熱設計的一個性能指標,LED 光輸出的許多屬性都取決于絕對結溫。
結-殼 (RthJC) 等單一熱阻值仍舊列于產品說明中,可用于元器件選型和早期設計階段。但是,散熱的復雜三維特性只能使用先進的仿真工具并結合熱測量進行預測。
為解決這些問題,業界開發出了瞬態熱測量方法,從而可提供比使用熱傳感器更好的解決方案。如今,為了能夠創建電子系統的最佳設計,需要精確提取熱特性。開發仿真模型時,熱特征提取技術有助于提供更好的結果。綜合使用熱特征提取、瞬態熱測試和三維熱建模,可以減少物理樣機的迭代次數、生產過程中的重新設計以及現場缺陷產品的召回,從而節省時間和成本。
基本意義上的瞬態熱測試是指對器件施加一個穩定的低功率電平,然后立即切換到較高電平以觀測加熱瞬態。同樣,從較高功率電平切換到較低電平,可以監測器件的散熱情況。這些瞬態可以完全被捕捉到,直至達到穩態。
結構函數:闡釋的革命
用于模型創建的瞬態熱測量的發展在科爾階梯網絡模型中達到巔峰。此模型對于將電路元件與物理區域進行關聯非常有用。模型描述的特性是利用“結構函數”識別熱流通路的基礎。布達佩斯大學的研究人員制定的結構函數分析方法,可滿足對封裝內部給出更多闡釋的需求2。Székely3引進了封裝半導體器件的熱測試方法,從而徹底改變了對熱測量的闡釋。于是,便創建出了Simcenter T3STER 瞬態熱分析軟件系統。
結構函數將瞬態熱測量結果轉換為熱阻與熱容的關系曲線,從而提供熱量經過的每一層(從結點到環境)的詳細熱信息。這樣就能確定固晶焊、基座、封裝、散熱器、乃至冷卻設備(如風扇)等各層的物理特性。
通過這種方法,工程師現在能夠識別單芯片封裝的固晶焊故障4
,生成散熱基板的動態簡化模型以加快電路板級設計5
,對 LED 封裝進行熱可靠性測試6
,甚至評估系統級熱性能,例如筆記本電腦或激光打印機。附錄介紹了將溫度-時間曲線轉換為結構函數的數學原理。
結構函數應用示例:界面熱阻的特征提取
LED 封裝的某些部分非常穩定(例如,芯片、基座、散熱塊)。然而,即便是相同制造批次的樣品,用于填充附著表面之間微小間隙的導熱界面材料 (TIM) 層也可能會顯示出很大的差異。測試 TIM 本身無法得知所制造的 TIM 層實際的熱阻。為了研究產品中的這些不可避免的差異,最好就是使用結構函數。
圖 1 顯示了 LED 應用中的典型導熱界面。其質量可通過沿熱阻軸的長度來衡量,如圖 2 所示。界面熱阻變化的原因可能有很多:固化/焊接溫度變化、TIM 層的厚度差異、老化或故意改變質量等。
圖 1.典型 LED 應用的結-環境熱流通路中的不同導熱界面。
圖 2.LED 元器件的微分(細線)和積分(粗線)結構函數。Rth基于加熱功率(針對光輸出校正的功率)1。
測量界面材料熱導率
圖 3.基于結溫瞬態測量的動態 TIM 測試設置1。
圖 4.動態 TIM 測試裝置的結構函數,在被測材料的不同預設粘結層厚度處測量1
在圖 3 所示的設置中,功率二極管的結溫瞬態 ΔTJ(t)是在精確規定的預定材料厚度(粘結層厚度 BLT)下測得的。當功率二極管發熱時,產生的熱量通過樣品進入下方的冷板。
當利用一個精密的專用機械系統變更樣品厚度時,整個測試設置的總熱阻測量結果會發生變化。圖 4 中的結構函數表明,測試設置的結-冷板總熱阻的變化完全是由材料樣品厚度的變化引起的。功率二極管的熱特性可以認為沒有改變,被測樣品任一側的界面熱阻也是如此。
樣品的熱導率 λ 可以按如下方式進行計算:
其中,A 為穿過樣品的熱流通路的橫截面積,ΔL 為粘結層厚度變化,ΔRth為測試設置總熱阻的相應變化。
根據這一方程,被測 TIM 樣品的熱導率與樣品的Rth
–BLT 圖的斜率成正比(圖 5)。
圖 5:在圖 3 所示的動態 TIM 測試設置中測量獲得的給定材料類型的熱阻與粘結層厚度的關系圖1。
同其他技術相比,這種 TIM 測試方法具有一些優勢。例如,微分法可減小測量的不確定性。該測試方法是一種準原位技術,因為測試夾具類似于 TIM 材料的實際應用條件。最后一個重要點是,每項測量都包括測量系統的固有自檢。基于所獲得的結構函數,總是可以檢查測試夾具的結構完整性。該方法已在 Simcenter DYNTIM 軟件8中實現,它會自動執行 TIM測試并利用結構函數方法進行瞬態熱分析。
通過校準提高熱模型精度
圖 6:芯片尺寸和有效(散熱)區域面積的校正9。
仿真模型最多只能與可用輸入數據(即器件幾何形狀和材料屬性)一樣好。這在為計算流體動力學 (CFD)仿真工具創建詳細模型時,始終是一個問題,哪怕是原則上至少應當知道器件幾何形狀的半導體供應商。但很多時候,材料參數以及有效體積或面積會引發一系列的問題。如前所述,詳細熱仿真模型中不確定性的一個可能來源是界面熱阻,包括 TIM1(固晶焊)和TIM2(例如導熱硅脂)兩個地方。
利用結構函數對詳細模型進行校準/驗證背后的理念是:如果仿真模型中的幾何形狀/材料屬性和邊界條件都符合實際情況,那么測量得到的熱阻抗曲線和仿真得到的熱阻抗曲線應當完全一致。因此,幾何形狀或材料失配造成的任何微小差異都應該能在相應的結構函數中看到。
下面的案例分析說明了如何在結構函數的幫助下對功率半導體器件封裝模型進行微調9:創建 BD-242 型晶體管(采用 TO-220 封裝)的經校準的詳細模型。
圖 7:固晶焊熱阻也獲得校正9。
圖 8:最終校準模型與調整后的 TIM2 熱阻9。
圖 6 到圖 8 顯示了調整仿真模型所采取的主要迭代步驟。在前期迭代階段中,應讓芯片尺寸和有效(散熱)芯片表面區域的面積相匹配。通過這種修改,熱流通路模型的第一部分獲得了修正(圖 6)。仿真的熱阻抗和測量的熱阻抗完全匹配,且累積熱阻值最高可達 2.5 K/W 左右。
在固晶焊層的特性也被修改后(通過調整 TIM1 材料的熱導率將界面熱阻設置為適當的值),結構函數完全匹配,最高達到約 4.4 K/W(圖 7)。
模型校準的最后一步是正確設置所用 TIM2 層的熱阻(圖 8)。由此,模型校準即告完成。剩下的差異要歸因于所用冷板的建模。
上述程序可利用 CFD 仿真工具 Simcenter Flotherm的軟件命令中心自動完成,該工具可使用 SimcenterT3STER 瞬態熱測試儀提供的數據。
結語
本文通過兩個例子討論了如何使用結構函數來分析半導體封裝內部的熱特性,或者說任何復雜電子系統的熱特性。結構函數還能用于其他應用,例如:獲得多芯片封裝的熱測量,在不同環境條件下對封裝中的TIM 進行系統內測試,利用溫度和功率循環為可靠性分析提供數據,以及測試交流驅動 LED 等。
現在可以提供這些功能的測試設備軟件包括:Simcenter T3STER 瞬態熱分析系統,用于分析 LED 的 SimcenterTERALED 軟件,用于測試 TIM 的 Simcenter DYNTIM,以及用于實驗室中或車間的功率循環和封裝測試的Simcenter Micred Power Tester 軟件。
審核編輯:劉清
-
功率二極管
+關注
關注
1文章
373瀏覽量
14595 -
半導體
+關注
關注
334文章
27697瀏覽量
222580 -
單芯片
+關注
關注
3文章
422瀏覽量
34666 -
散熱器
+關注
關注
2文章
1057瀏覽量
37752 -
LED封裝
+關注
關注
18文章
359瀏覽量
42228
原文標題:復雜電子設備的熱表征:結構函數基礎入門
文章出處:【微信號:BasiCAE,微信公眾號:貝思科爾】歡迎添加關注!文章轉載請注明出處。
發布評論請先 登錄
相關推薦
復雜醫療電子設備的的設計保護
電子元器件基礎知識(324頁)
結構函數的由來及推導過程
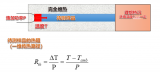
功率器件熱設計基礎(十)——功率半導體器件的結構函數
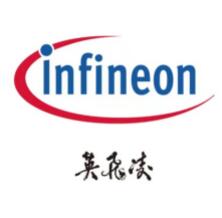
評論