摘要
為滿足快速發展的電動汽車行業對高功率密度 SiC 功率模塊的需求,進行了 1 200 V/500 A 高功率密度三相 全橋 SiC 功率模塊設計與開發,提出了一種基于多疊層直接鍵合銅單元的功率模塊封裝方法來并聯更多的芯片。利用互感對消效應減小寄生電感,導電面積增加了 1 倍,因此可以減小功率模塊的總面積。在電磁學與熱力學仿 真分析的基礎上,進行了實物制作與性能測試。仿真與實驗結果表明:與傳統的封裝方法相比,該封裝方法減少 了 34.9%的尺寸,并減少了 74.8%的寄生電感使得門極具有更高的穩定性,且當直流 300 A 電流時,單相最高結溫 為 158 ℃。
如今,三相全橋功率模塊廣泛應用于電動汽車 與工業驅動領域,并對功率密度提出了越來越高的 要求。為了實現更高的功率密度,須提高功率模塊 的開關頻率,降低雜散電感,還要增強散熱能力。隨著寬禁帶功率器件的不斷發展,碳化硅(silicon carbide,SiC)由于其更高的擊穿電壓,更高的工作溫 度,更低的開關損耗,顯示出取代硅基功率器件的 巨大潛力。然而由于封裝限制,這些突出的優點目 前還無法在同尺寸的功率模塊中得到有效證明。
二維引線鍵合封裝結構工藝已經相對成熟且簡 單,因此在商用 SiC 功率模塊設計中得到廣泛應用。但是這種二維的功率模塊封裝結構通常具有較大的寄生電感,這很大程度上限制了SiC 器件的開關速 度。這種寄生電感的存在還會導致造成門極的不穩 定振蕩,阻礙了功率密度的進一步提高。Chen 等提出了一種改進的線鍵結構,用于 1200 V/60 A SiC 功率模塊,在二維模塊中采用疊層引線框架, 增強開爾文源極對稱性來降低寄生電感。Huber 等提出了一種多直接鍵合銅(direct bonding copper, DBC)的 600 V/200 A 單相全橋 SiC 功率模塊,采用 兩層 DBC 實現了低寄生電感,功率器件焊接在雙層 DBC 的頂層。Luo 等基于疊層 DBC 開發了 1200 V120 A 的半橋 SiC 功率模塊。然而,對大功率下三相全橋的疊層 DBC 功率模塊的研究相對較少,特別 是在面對更大電流和更高功率的情境下,對于疊層 DBC 功率模塊芯片熱穩定問題的深入研究尚需進 一步展開。
基于上述分析,本研究提出了一種多疊層 DBC 單元的封裝結構,并研制了 1 200 V/500 A 三相全橋功率模塊,該模塊利用 pinfin 散熱器進行水冷散熱, 并進行了電氣性能與散熱性能仿真與實驗。
1 功率模塊設計和仿真
1.1 疊層 DBC 單元設計
疊層 DBC 封裝結構側面圖如圖 1 所示,底部 DBC 和頂部 DBC 分別傳導電流,SiC MOSFET 芯 片的漏極焊接在底層 DBC 上,門極與源極通過鍵合 線與頂層 DBC 相連接。
互感抵消效應如圖 2 所示,疊層 DBC 的電流 路徑重疊且方向相反,該設計采用了互感抵消效應, 通過使電流在相鄰層之間反向流動,顯著降低寄生 電感,這一技術在疊層母排設計中已經得到廣泛應 用。相相對于傳統的二維封裝結構,這種方法可以 有效降低雜散參數,從而改善功率模塊的整體性能。
疊層 DBC 單元及電流流通路徑如圖 3 所示, 尺寸為 59 mm × 32 mm。通過在 Ansys Q3D 中提取 寄生電感,該功率模塊的總寄生電感僅為 4.74 nH。相較之下,具有相同額定功率和尺寸為 64 mm×44 mm 的傳統二維布局模塊的寄生電感值為 18.84 nH。
由于電流路徑增加了 1 倍,因此在相同的封裝 面積下,疊層 DBC 單元允許更多的芯片并聯,從而 顯著增加了 SiC 功率模塊的功率密度。這種方法工 藝相對簡單,有望降低生產成本,提高生產率。如 圖 4 所示,最終設計的 1200 V/500 A 高功率密度三 相全橋 SiC 功率模塊的尺寸與 EconoDUAL 封裝的 商用單相全橋模塊一致。
1.2 散熱設計
冷卻系統在電力電子系統的總質量和總體積 中占據相當大的比例。為了實現更高的功率密度, 功率模塊通常采用 PinFin 散熱器來提升散熱性能。本研究所采用的 PinFin 散熱器結構圖 5 所示,這種 結構在相對較小的空間內提供了更大的散熱表面積, 使其與周圍環境更有效地交換熱量,從而提高了整 體散熱性能。
計算流體力學(computational fluid dynamics, CFD)仿真模型根據所需工況設置每顆芯片功率 150 W,三相模塊總熱耗率為 5 400 W。入口水流速 為 0.52 m/s,水溫 25 ℃,出口壓力為靜壓,本研究 設計的功率模塊各部分材料參數如表 1 所示。仿真 結果如圖 6 所示,根據仿真結果分析,芯片最高結 溫 148.42 ℃,芯片平均結溫 123.24 ℃。最高結溫和 平均結溫的數據有助于評估功率模塊散熱設計的性 能,驗證提出疊層 DBC 單元封裝結構的可行性。
2 實驗驗證
2.1 模塊制作
功率模塊封裝工藝制作流程如圖 7 所示,首先 是芯片出廠檢測與功率模塊封裝的設計,之后進行 芯片濺射、真空焊接、超聲波焊接和模塊真空灌封, 最后進行模塊的檢測。在制作流程中,芯片的出廠 檢測和功率模塊的封裝設計確保了所使用的芯片質 量可靠且符合設計要求。芯片濺射、真空焊接、超 聲波焊接等工藝步驟用于將芯片按照電路拓撲連接 到封裝結構中。模塊真空灌封則有助于提高封裝的 密封性,確保內部芯片在惡劣環境中的可靠運行。圖 8 展示了設計的 1 200 V/500 A 高功率密度三相 全橋 SiC 功率模塊的實物。
2.2 電氣性能測試
開關器件的動態電氣性能可以通過雙脈沖電路 獲得,下管用作被測器件。柵極-源極電壓 Vgs 與漏極-源極電壓 Vds 使用高壓隔離差分探頭測量,漏極 電流 Id 使用羅氏線圈電流探頭測量。上管的柵極承 受負電壓,因此上管關閉,只有續流二極管在工作, 由圖 9 所示的測試結果波形可以看出,制作的功率 模塊通過了 800 V/500 A 的雙脈沖測試,證明了所 提出的功率模塊在高電壓和大電流條件下具有可靠 的動態電氣性能,符合設計和規格要求。
傳統的二維封裝結構由于雜散電感更高,在電 流為 200 A 時門極已經出現了明顯振蕩,如圖 10 所 示。
門極振蕩可能導致不穩定的工作狀態,與之相 比,本研究使用的疊層 DBC 封裝結構通過減小雜散 電感,提高了功率模塊的動態性能。
2.3 散熱性能測試
為了更全面地評估功率模塊的散熱能力,采用 功率模塊單相全橋直通的方式,通過紅外熱成像儀 對功率模塊進行觀察,以獲取功率模塊的最高結溫。測試實驗環境如圖 11 所示,其中弱電電源為門極驅 動供電,電流源提供大電流。最終測試功率模塊直 通電流值為 300 A。圖 12 為 300 A 時功率模塊熱分 布結果圖,根據結果可知,在這種條件下,功率模塊單相最高結溫約為 158 ℃左右。這一實驗結果提 供了對功率模塊在大電流通流情況下的實際工作狀 態的直觀了解,為優化散熱設計和確保功率模塊的 可靠性提供了參考,證明了大功率下本研究提出的 疊層 DBC 功率模塊設計的可行性。
3 結論
本研究針對電動汽車與工業驅動領域,設計并 開發了一款 1 200 V/500 A 高功率密度三相全橋 SiC 功率模塊。提出的采用多疊層 DBC 單元的設計方 法,簡化了制造流程,降低了成本,可以提高生產 效率。基于仿真結果進行了實物的設計與制作,并 進行了電氣和散熱性能測試。結果表明:相較于傳 統封裝方法,提出的封裝方法在尺寸上減小了 34.9%,寄生電感減少了 74.8%,使得門極具有更高 的穩定性。在直流 300 A 電流通流的情況下,單相 最高結溫為 158 ℃。本研究提出的三相全橋 SiC 功 率模塊設計方法有助于推動電動汽車電機驅動系統 功率密度的提高。
審核編輯:劉清
-
電動汽車
+關注
關注
156文章
12186瀏覽量
232444 -
散熱器
+關注
關注
2文章
1057瀏覽量
37753 -
SiC
+關注
關注
29文章
2886瀏覽量
62935 -
功率模塊
+關注
關注
10文章
475瀏覽量
45224 -
寄生電感
+關注
關注
1文章
156瀏覽量
14630
原文標題:高功率密度三相全橋 SiC 功率模塊設計與開發
文章出處:【微信號:芯長征科技,微信公眾號:芯長征科技】歡迎添加關注!文章轉載請注明出處。
發布評論請先 登錄
相關推薦
CISSOID、NAC和Advanced Conversion三強聯手開發 高功率密度碳化硅(SiC)逆變器
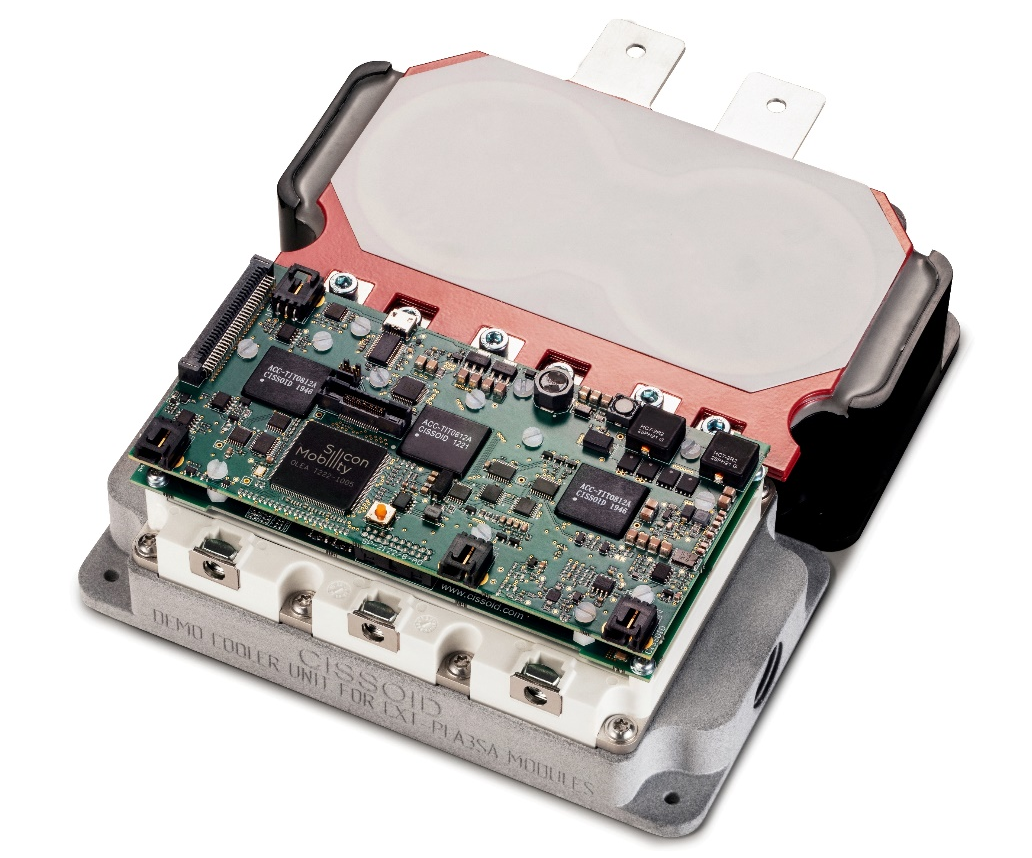
評論