0 引言
印制電路板(printed circuit board,PCB)在電子信息產業鏈中扮演著至關重要的角色,其應用遍及消費電子、通信設備、汽車電子、工控設備、醫療電子、航空航天和軍工等多個領域。所有帶有電路或電氣控制的設備或產品都依賴于PCB來實現元器件間的互連互通,從而發揮其功能。因此,PCB的質量直接關系到電子整機或系統產品的質量和可靠性,對電子行業至關重要。
過去約40年中,PCB產業經歷了從美國到日本,再到中國的轉移。自2016年以來,中國PCB產值規模在全球的占比始終保持在50%以上,2021年更是達到了570億美元,其中中國大陸本土制造商約占340億美元,產值規模占比提升至近60%。隨著國內5G通信、新能源(汽車、光伏、風電等)、大數據、集成電路、人工智能、物聯網等下游行業的快速發展,以及產業鏈配套和綜合成本的優勢,國內PCB行業市場前景廣闊,預計全球市場份額將進一步提升。中國作為全球最重要的PCB生產基地,未來將繼續保持行業制造中心地位。然而,國內PCB行業雖“大”,卻“不強”,行業內低水平重復競爭激烈,影響了行業的良性發展和國際競爭力。與國外相比,在高端PCB制造技術方面還存在差距,特別是在工藝路線穩定性和產品可靠性、一致性等方面有較大的提升空間。
1板卡失效因素分布
板卡,即完成元器件組裝的PCB,簡稱印制電路組件(printed circuit board assembly,PCBA)。對引起板卡失效的因素進行統計分析,如圖1所示,發現PCB自身失效導致板卡失效的案例占比51%,超過PCBA本身制程缺陷引起的焊點虛焊(由焊接工藝本身異常引起)或開裂(由過應力或疲勞等應用環節引起)和焊點腐蝕、遷移或離子殘留(分別占比18%、9%,合計占比27%)、應用過程由過應力或疲勞引起的焊點開裂失效(占比12%)和其他類失效10%的總和。PCB自身質量異常已成為引起PCBA失效的最主要原因。
圖1 PCBA失效因素分布
2PCB失效模式總體分布
圖2 PCB各類失效模式總體分布
對PCB自身失效案例進行統計分析,列出12項失效模式類型,如上圖圖2所示。前4大失效模式依次為導通失效(26.6%)、可焊性不良(22.3%)、分層爆板(17.5%)和絕緣失效(15.3%),合計占比為81.7%。第5大失效模式燒板和第6大失效模式焊接強度不足分別占比5.3%和4.2%;涂/鍍層異常、板面異色、PCB翹曲、剝離強度不足、鍵合不良等其他類型的失效模式合計占比為8.8%。進一步對2019—2021年度中每年的PCB失效案例數量進行統計,如圖3所示,并按其失效模式類型進行分析,發現失效案例數分別為96、123和140個,呈現逐年增加的趨勢;導通失效、可焊性不良、爆板分層和絕緣失效4種失效模式合計占比連續3年都在80%以上;導通失效連續3年都為年度占比最高的失效模式,年度占比最高達到31%;可焊性不良、爆板分層和絕緣失效3種失效模式年度占比排名略有差異,但連續3年都位于第2~4名。導通失效、可焊性不良、分層爆板和絕緣失效成為國內PCB行業最為常見的4大失效模式,也是亟待改善的質量和可靠性問題。
圖3 2019年—2021年PCB失效模式分布
針對失效模式占比最高的導通失效,進一步根據導通互連結構進行細分,發現孔銅開路、內層互連開路和導線開路占比分別為69%、21%和10%,孔銅開路的失效比例遠遠高于另外2種類型,這說明PCB的通孔、盲孔或埋孔是導通互連質量的薄弱環節,需重點關注,如下圖圖4所示。針對第2大失效模式可焊性不良,按表面處理工藝進行細分,發現熱風焊料整平(hot air solder leveling,HASL)、化學鍍鎳/浸金(nickel/immersion gold,ENIG)和有機可焊性保護膜(organic solderability preservative,OSP)引起的可焊性不良分別占比38%、37%和7%,通孔可焊性不良占比11%,其他類型合計占比7%。說明HASL和ENIG處理2類是最易出現PCB可焊性不良的問題,這可能與HASL處理鍍層厚度不均及合金化(圖5)、ENIG中鎳層易氧化或腐蝕(圖6)有關,PCB企業應對相關制程進行重點管控。
圖4 PCB 孔銅開路典型案例
圖5 HASL 工藝合金化引起可焊性不良的典型案例
圖6 ENIG 工藝中鎳層腐蝕的典型案例
3 不同排名PCB企業失效情況
對PCB自身失效案例中PCB制造廠家信息進行梳理,按照中國電子電路行業協會(China Printed Circuit Association,CPCA)發布的《第二十屆(2020)中國電子電路行業之綜合PCB前100家企業》中企業排名情況,對位于不同排名的內資PCB企業送檢失效案例的數量分布進行統計,結果如圖7所示。排名1~25、26~50、51~75、76~100的PCB企業失效案例數量占比分別為17%、10%、14%和7%,排前100名的企業累計數量占比為48%,說明PCB產品失效在大中型企業也是較突出的問題。由于前100名企業包含了國內的主要PCB上市公司,在規模、管理和技術體系等方面相對更為完善,且代表國內PCB制造技術水平,相關失效的發生會直接影響著客戶的滿意度和企業的口碑,需特別予以關注。
圖7 不同排名PCB企業失效案例數量占比分布
對排前100名內資PCB企業發生的失效案例按照其失效模式類型進行統計分析,結果如圖8所示。前4大失效模式依次為可焊性不良(27.6%)、導通不良(24.3%)、分層爆板(14.8%)和絕緣失效(8.9%),合計占比為75.6%。這與PCB行業前4大失效模式一致(圖2),說明大中型企業PCB產品面臨的質量問題與國內整個行業情況類似。
圖8 排前100名PCB企業各類失效模式分布
4 軍/民用PCB失效模式分布
2019—2022年,軍用PCB質量問題引起整機裝備失效的案例呈逐年增長的趨勢。原因為裝備的質量與可靠性要求不斷提高,更容易激發出相關問題;另一方面與對PCB質量管理總體重視程度不夠有關。部分整機單位甚至把PCB當做“零部件”而非關鍵元器件管理,沒有建立類似于元器件從選型、篩選、破壞性物理分析(Destructive Physical Analysis,DPA)到失效分析的全套閉環質量管理流程。對軍用PCB失效案例按照其失效模式類型進行統計分析,結果如圖9所示。軍用PCB導通失效模式占比49%,接近一半,遠高于其他失效模式,緊隨其后的是分層爆板(12%)、燒板失效(11%)、可焊性不良(9%)和絕緣失效(9%),這5大失效模式為軍用PCB的主要缺陷問題,約占90%;其次是翹曲失效(3%)、異色(3%)等失效模式。
圖9軍用PCB失效模式分布
對民用PCB失效案例進行統計分析,結果如圖10所示。民品PCB的前4大失效模式依次為可焊性不良(25%)、導通失效(22%)、分層爆板(19%)和絕緣失效(17%),占總失效案例數量的83%;其次是焊接強度不足(5%)、燒板(4%)、涂/鍍層異常(3%)、異色(2%)等失效模式。
圖10 民用PCB失效模式分布
對比軍用PCB和民用PCB的失效模式分布可以看到,導通失效和可焊性不良都是PCB最為突出的問題。原因為軍用PCB應用環境更為嚴苛,在經過例如溫度沖擊、濕熱循環、振動沖擊、高低溫工作/貯存等一系列實驗室模擬或實際應用條件后,PCB的線路、孔銅、內層互連界面等容易產生更大的溫變、機械和疲勞等應力,造成導通網絡發生開路失效。另一方面與軍/民PCB質量檢測手段差異也有關,民用PCB貼件后普遍采用的自動光學檢測(Automated Optical Inspection,AOI)檢測手段,更易在服役應用階段之前就發現外觀可焊性不良的問題(即便尚未造成功能異常)。軍用PCB板大多數質量問題都是板卡功能異常后的逆向分析發現,直接引起功能異常的失效模式(如導通失效、分層、燒板等)更容易被送檢分析。
(未完,接下篇)
審核編輯 黃宇
-
pcb
+關注
關注
4326文章
23161瀏覽量
399970 -
激光
+關注
關注
19文章
3251瀏覽量
64853
發布評論請先 登錄
相關推薦
大研智造激光焊錫機:霍爾傳感器PCB電路板引線焊接的“完美解”?
大研智造激光焊錫機,如何點亮微小點狀激光模組PCB焊接新未來?
焊錫機廠家大研智造:引領錫球焊錫機和全自動焊錫機發展的“領航者”
大研智造激光焊錫機:為BGA封裝提供高效焊接的智能化選擇
超越傳統焊接:大研智造激光焊錫機在電纜組裝件制造中的應用
大研智造 激光焊錫機:電子組件微型化與高密度焊接的解決方案
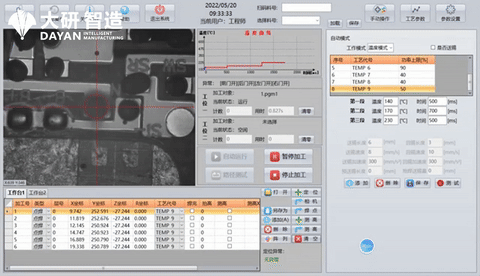
評論